Program Elements
Program Inspections
Program inspections are a vital part of maintaining machine safety in the workplace.
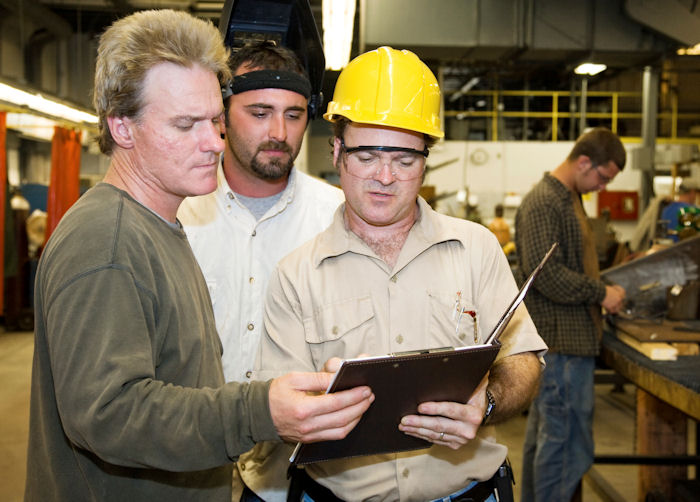
Regular inspections help identify hazards, ensure that safeguards are functioning correctly, and prevent accidents before they occur. Proper assessment and documentation also support compliance with safety regulations and continuous improvement of safety practices.
Inspection Processes:
Inspection processes generally involve examining machine and/or equipment for potential and existing hazards. Open the link below to review typical machines, equipment, and related hazards that require inspections.
Location | Machines/Equipment | Hazards |
---|---|---|
Machine Shops | Metalworking tools: shears, brake presses, drill presses, lathes, mills, grinders, etc. | Machine motions and actions, shafts, belts, pulleys, flying objects |
Wood Shops | Woodworking equipment: tablesaws, bandsaws, lathes, skillsaws, planers, jointers, drill presses, etc. | Machine motions and actions, shafts, belts, pulleys, flying objects |
Mechanical Rooms | Boilers, pumps, compressors | Belts, pulleys, power transmission equipment |
Roofs | HVAC, planums, fans | Shafts, pulleys, belts |
Shipping/Receiving | Conveyors | Belts, rollers, chain drives, gears |
Waste Treatment | Pumps, mixers, separators | Shafts, pulleys, belts |
Packaging Areas | Palletizers | Reciprocating, hydraulic "sweeping" arms, chain drives, belts |
Production Floor | Power presses, punch presses, conveyors, packages, robotics | Machine motions and actions, shafts, belts, pulleys, flying objects, stroking action, material feeding and ejection |
- Initial, Follow-up, and Periodic Inspections:
- Conduct a thorough inspection when new equipment is installed to verify all safeguards are correctly installed and functioning.
- Ensure that all moving parts are guarded according to safety standards before operation begins.
- Inspect machines after any modifications, repairs, or adjustments to confirm safeguards remain effective and intact.
- Verify that changes do not introduce new hazards or reduce existing protection.
- Perform periodic scheduled inspections, typically on an annual basis, to maintain ongoing safety and compliance.
- Check for wear, damage, or removal of guards and safety devices.
- Observe operator adherence to safety procedures related to machine guarding.
- Incident and Near-Miss Inspections:
- Immediately inspect equipment after any accident, injury, or near-miss to identify causes and prevent recurrence.
- Document findings and implement corrective actions promptly.
- Documentation and Record-Keeping:
- Maintain detailed records of all inspections, findings, and corrective actions taken.
- Keep records for a minimum of five years to comply with regulatory requirements and support audits.
- Use documentation to track recurring issues and improve safety programs over time.
- Assignment of Responsibility:
- Designate qualified safety professionals or trained personnel to conduct inspections and oversee machine safeguarding programs.
- Ensure clear roles and accountability for inspection schedules and follow-up actions.
- Integrate inspections into a proactive maintenance program to address hazards before they cause harm.
Knowledge Check Choose the best answer for the question.
7-9. According to the Machine Guarding Safety Program, why should inspections be done after repairs or modifications to machinery?
You forgot to answer the question!