Warnings
With the release of ANSI Z10-2012, "warnings" have been promoted to their own hierarchy level. Previously they were considered part of administrative controls.
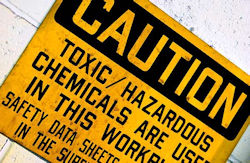
Warnings do not prevent exposure to a hazard, but they do provide information to warn people of potential danger. They work only when employees comply with the warning or caution.
Warnings can be either visual, audible, or both. They may also be tactile. Some examples of warnings are:
- Visual. Signs, labels, tags, and flashing/strobe lights.
- Audible. Alarms, bells, beepers, sirens, announcement system and horns.
- Tactile. Vibration devices or air fans.
Work Practice Controls
Work practice controls are mandatory procedural and practices designed to reduce or prevent exposures to ergonomic risk factors.
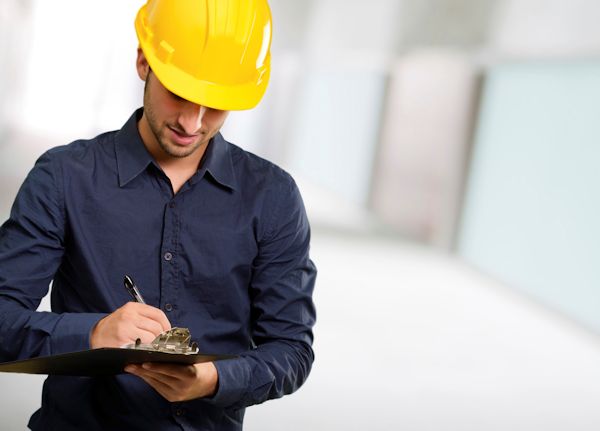
Although engineering controls are preferred, work practice controls can be helpful when engineering controls are not technically feasible. However, since work practice controls focus on eliminating or reducing exposure (not the hazard itself), they require diligent management, training, supervision, and enforcement to be effective. Bottom line: Work practice controls work only as long as employees comply with them.
Common examples of work practice control strategies for reducing the risk of MSDs are as follows:
- Reducing shift length or curtailing the amount of overtime
- Rotating workers through several jobs with different physical demands to reduce the stress on limbs and body regions
- Scheduling more breaks to allow for rest and recovery
- Broadening or varying the job content to offset certain risk factors (e.g., repetitive motions, static and awkward postures)
- Adjusting the work pace to relieve repetitive motion risks and give the worker more control of the work process
- Training in the recognition of risk factors for MSDs and instruction in work practices that can ease the task demands or burden
Knowledge Check Choose the best answer for the question.
5-4. What is a major weakness of using work practice controls to mitigate ergonomic hazards?
You forgot to answer the question!